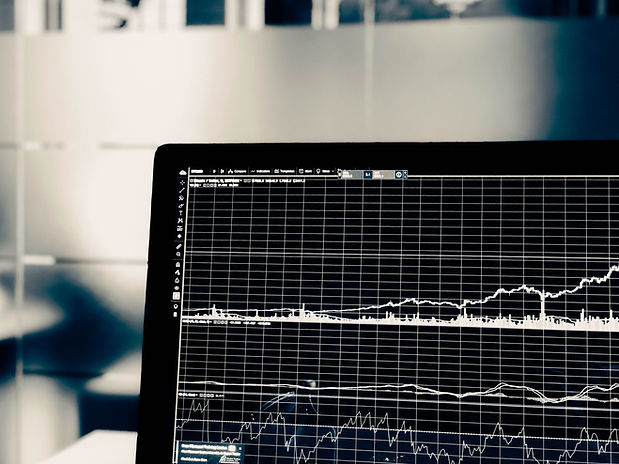
Stock Control
It is a mandatory requirement all entrants to the Food Production Unit understand and abide by all of FERA LTD Policies & Procedures.
|
|
Document Reference Number | 1.7 |
Document Sub-Sections |
|
Issue Number | 1.0 |
Issue Date: | 05/01/2024 |
Last Reviewed Date | 05/01/2024 |
Reviewed by | Board of Directors |
Next Review Date | Annualised 05/01/2025 (Earlier if any significant changes made or required). |
Responsible Officer(s) | Board of Directors |
Distribution |
|
Storage | Stored on the intranet. |
Document Control | Uncontrolled Copy Unless Printed on Yellow Signed Paper or accessed on intranet. |
Amendments with date of amendment. | Nil |
Document Notes | Nil |
Intranet Link | |
Authorised by | Adeel Iqbal |
1.7.1a STOCK CONTROL POLICY AND PROCEDURES
Stock control is a term used to describe the measures taken to ensure that food is not kept beyond its shelf life. If stock control is not properly implemented harmful bacteria can multiply rendering food unsafe.
Proper stock rotation ensures that all food is sold and used before its expiration.
To ensure that this works and food is safe for the consumer to enjoy the policies in this document must be followed by everyone who handles any food items.
FERA uses the FIFO – First-In First-Out system of stock control.
1.7.1b ENSURING STOCK IS SOURCED FROM REPUTABLE SUPPLIERS
FERA shall ensure that products are bought only from reputable suppliers that meet our supplier approval policy and regularly audited.
Our food items must be regularly checked to ensure no contamination from microbiological, physical, chemical or allergenic sources. Use the FIFO principles. Staff are trained in FIFO principles
1.7.1c FIRST IN FIRST OUT STOCK ROTATION PRINCIPLE
FIFO stands for First-In First-Out. It is a stock rotation system used for food storage.
You put items with the soonest best before or use-by dates at the front and place items with the furthest dates at the back.
By using a FIFO food storage system, you ensure that food with the nearest best before or use-by dates are used or sold first.
The FIFO procedure follows 5 simple steps:
Locate products with the soonest best before or use-by dates.
Remove items that are past these dates or are damaged.
Place items with the soonest dates at the front.
Stock new items behind the front stock; those with the latest dates should be at the back.
Use/sell stock at the front first.
FIFO is a continuous process. When new stock comes in, always use the FIFO procedure to store stock.
1.7.1d STOCK CONTROL AND LABELLING RE-WORK OR CHANGING CONTAINERS
If you remove any date product from its original packaging into a new container you must label the new packaging to include:
Product Name and Details
The date it was opened
The best before of the product
Your name and signature
1.7.1e SUPPLIERS AND SPECIFICATIONS / MINIMUM SHELF LIFE ON DELIVERY
FERA carries out yearly supplier audits via our supplier audit questionnaire.
Within the audit we ask our suppliers about minimum acceptable shelf life on delivery.
On each delivery we will confirm with our suppliers, including via written Purchase Orders where necessary, what the minimum remaining shelf life will be on delivery of the product.
1.7.1f REGULAR STOCK CHECKS INCLUDING QUANTITY OF ITEMS, LOCATION AND EXPIRY ARE MONITORED AND RECORDED
We regularly check stocks of all items including completed items, raw materials, packaging, supplementary materials and expired items usually on a weekly basis and this is recorded in the stock management folder.
STOCK CONTROL DOCUMENT | Click on FERA INTRANET footer |
1.7.2 SURPLUS LEVELS OF STOCK, OR STOCK NOT MEETING SPECIFICATIONS POLICY
We do not sell, donate or forward expired, surplus stock or items that do not conform to our standards or specifications.